Standard Abrasives™ A/O HD Unitized Wheel 863178, 631 6 in x 1 in x 1 in, 3 per case
-1
SKU: 7100080333
Standard Abrasives™ A/O HD Unitized Wheel 863178, 631 6 in x 1 in x 1 in, 3 per case
SKU: 7100080333
$87.09
/ Each
Add $199.00 worth of items to your cart to qualify for 

Minimum Order Quantity: 3 Each
QTY:
SHIPPING DIMENSIONS
Height: 3.69 Inches
Width: 6.38 Inches
Length: 6.38 Inches
Weight: 1 Lb(s) 12 Oz
Technical Specifications
- Soft/Medium density wheel blends surfaces to a nice finish
- Increased edge durability over the 500 Series offers better cut and adds life for light deburring and blending applications
- Aluminum oxide mineral is a good match for ferrous and non-ferrous metals, including aluminum
- Runs clockwise and counterclockwise, allowing greater versatility when paired with tools and machines
- Open web is load resistant, contributing to longer abrasive service life
- Center hole wheel attaches to tool with a unitized wheel mandrel (sold separately)
More Product Details
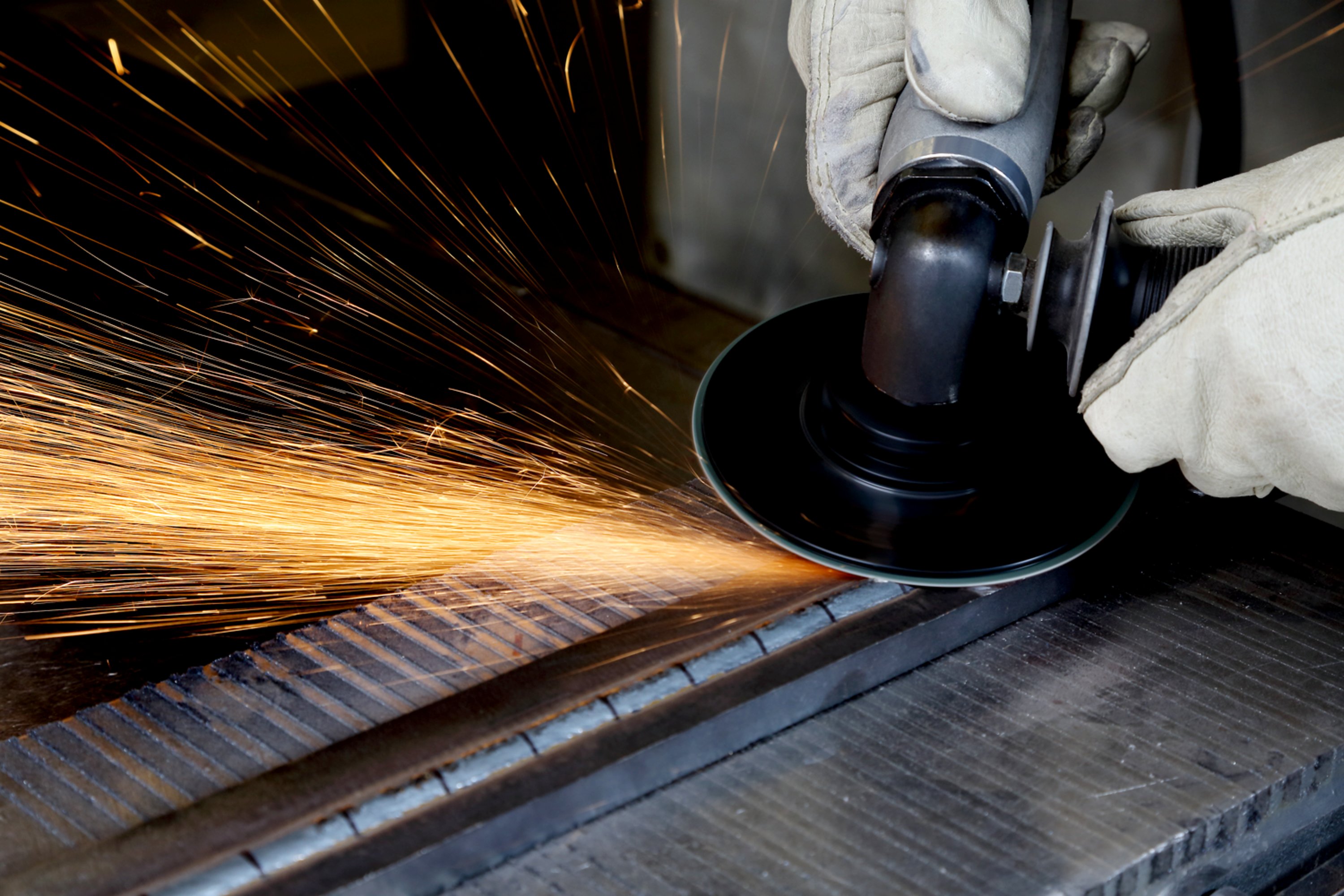
Soft/Medium density wheel offers exceptional conformability and blends surfaces to a smooth finish
The Standard Abrasives™ Aluminum Oxide (A/O) HD Unitized Wheel 600 Series has a soft to medium density when compared to other wheels in the Standard Abrasives™ Unitized Wheels line, and is designed with increased edge durability over the 500 Series wheels. Constructed with fine grade aluminum oxide, this double-duty abrasive combines durability with a fine scratch pattern, making it a great choice for projects that require an aggressive cut yet soft finish — namely, tough blending and light finishing applications.
Use the Standard Abrasives™ A/O 600 Series HD Unitized Wheel for blending and refining surfaces of jet blade airfoil, blending parting lines from cast turbine blades and vanes, blending stainless steel surgical instruments, mill marks and machine mismatches and removing minor pits, scratches, resins/adhesive overspray, coating and plastic mold flashing. They are a good match for polishing fillet areas on jet blades and soft metals prior to the coating process. They may also be used on softer metals for light deburring and edge radiusing. Due to their conformability, these wheels are great for projects with strict tolerances, because they respond to surface irregularities. After prolonged use, the wheel can be dressed to maintain its shape.
Compatible with a Variety of Tools
Unitized wheels are typically used on a die grinder. A benefit of unitized wheels is that they are bi-directional and can be mounted on a tool or pedestal grinder without regard to the direction of the spindle rotation. This means the Standard Abrasives™ Unitized Wheel can be used with a variety of tools, and regardless of which way the workpiece is fed through the machine, the wheel will be able to respond, giving operators more flexibility. The stiffness of the unitized construction enables operators to use thinner wheels to access awkward angles with grinding tools.
Series 600 wheels require a unitized wheel mandrel (sold separately) for attachment to the tool. Quick change wheels are also available (sold separately).
Non-Woven Unitized Construction Offers a Step Up in Density and Durability for Stubborn Surfaces
Standard Abrasives™ Unitized Wheels are a great match for tough deburring, cleaning, blending and finishing applications. They come in a broad range of densities and grades to suit different metals, the degree of aggressiveness required, shape of the part, and desired finish. Although used for some of the same tasks as Standard Abrasives™ Buff and Blend products, they are designed with a far stronger and denser construction to support more aggressive applications and accomplish material removal more rapidly. Even though unitized wheels are much stiffer products, the non-woven nylon fibers of the wheel maintain the advantage of responding to surface irregularities while preserving the geometry of the piece, and produce a consistent finish.
Unitized wheels are created by starting with layers of open web material that combines non-woven fiber strands and abrasive mineral with a tough resin bond. These layers of web are then cured and compressed together. By fusing layers of open web, the abrasive gains more toughness and durability